Update on 3D-MID
Ultrashort Pulse Laser
Laser structuring with subsequent metallization is one of the most common processes in the manufacture of 3D-MID parts. When it comes to laser structuring, a distinction is made between Laser Direct Structuring (LDS), Laser Subtractive Structuring (LSS), Laser Structuring – Chemical Activation (LS-ChA) and Photo-Chemical Structuring (Ph-Ch-S).
The above currently used processes follow different principals and each of them has its pros and cons. Most of these processes operate in the nano second range; however, there are some disadvantages associated with this. Ongoing developments show that the ultrashort pulse laser would be the better alternative for some of these processes.
In this article Waldemar Honstein, our laser specialist and one of the pioneers of LDS technology, will explain some interesting effects of laser structuring using Ultrashort pulse laser. I hope you enjoy reading it (kind regards/Nouhad)
Ultrashort pulse lasers in modern material processing
Ultra-short pulse lasers have become an indispensable part of modern material processing. Whether you are cutting, engraving or marking, you will find a selection of systems, that are using ultrashort pulse lasers, which can be applied to your application. Those new lasers open up new possibilities for effective material processing. Whether plastic or metal, glass or diamond materials, these can be structured by a pico- or femto-laser.
What is so special about the picosecond and femtosecond lasers?
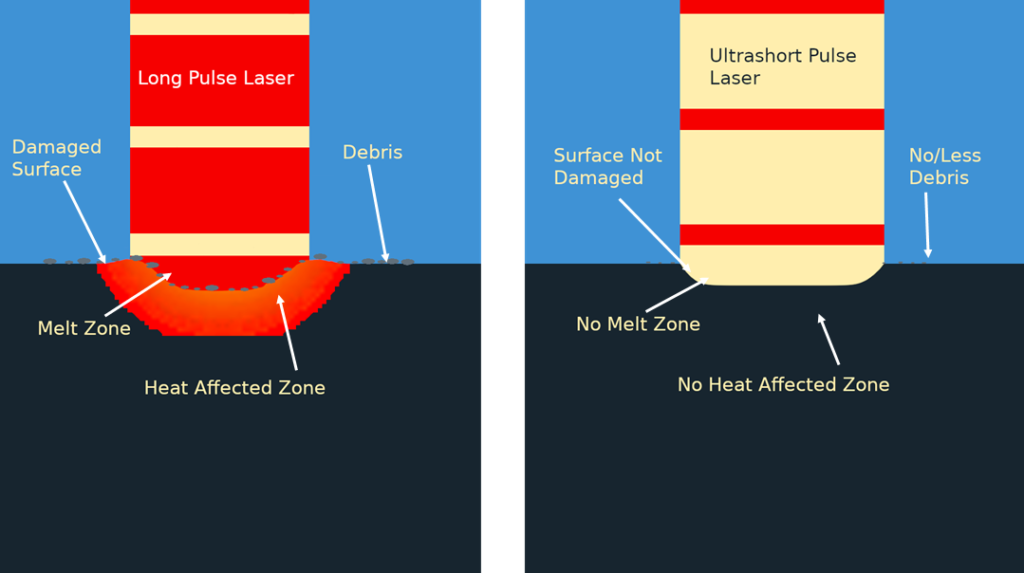
Regardless of what type of processing you use the laser for, traditional lasers heat the processed materials locally. Not only the processed area is thermally heated and modified in the process, but also adjacent areas. Depending on the application, to compensate for this, additional, complex processing steps may be necessary. In the worst case, if the thermal damage is inadmissible, instead of a laser process another, more expensive processing method must be utilized. Due to very short but high-energy pulses, the modification of the surface works with practically no heat input. Since there is no heat input, there is also no thermal damage to the adjacent areas and thus no reduction in the quality of the processed surfaces.
What is the benefit of using ultrashort pulse laser?
Analogous to other technologies, the advantages of an ultrashort pulse laser can also be advantageous for the 3D MID technology. Precise and clean structures on the substrate are crucial for quality and have an impact on subsequent processes. Here are some advantages of :
- Certain materials are sensitive to the input of heat. In order to avoid the thermal degradation of materials, processing parameters need to be adjusted accordingly, which usually results in longer processing times. With an ultrashort pulse laser there would not be such a restriction
- Thermal intake causes fraying edges of lasered surfaces. Ultrashort pulse lasers would create much cleaner edges here
- Drilling vias is a complex process because, on the one hand, the thermal input enables material to be removed and, on the other hand, the surrounding material must not be overheated. Achieving this balance usually results in long structuring times. A pico or femto laser would drastically reduce the processing time as well as improve the via quality.
Author: Waldemar Honstein
