Update on 3D-MID
Product robustness and reliability against environmental life tests
This is the first post in a series of articles on the topic “update on 3D-MID”. The series of articles will cover the entire MID environment: processes, materials, manufacturing equipment, quality, costs, applications, business development, current and future developments, etc. I chose reliability as the first topic because it is one of the most burning issues, and because frequent failure in the field is a death sentence for a technology.
Is reliability still an issue even though the technology has been in use for several decades? The answer to this question is, as engineers always say, it depends:
– No, if the requirements are low, as would be the case with consumer products that have a lifespan of 2 to 3 years, and only have to withstand the high temperature / high humidity test with 65 ° C / 90% RH / 72h
– Yes, when it comes to high automotive requirements, e.g. high temperature / high humidity test with 85 ° C / 85% RH / 1000h or 1000 cycles between -40 ° C and 140 ° C. Only a few materials like PEEK and LCP could withstand such tests in the past.
Peek is very expensive; LCP is a little less expensive, but not exactly cheap either. In addition, LCP also has its Achilles heel, namely the formation of welding lines that almost serve as a breaking point for the plated traces. One tries to avoid these welding lines when designing circuits, but that is not always possible. In addition, under certain circumstances, LCP tends to form bubbles or even ablation of the metal layer.
What about other engineering thermoplastics such as poliyamides? The effect here is much more serious due to the large differences between the coefficients of thermal expansion (CTE) of the poliyamide material in comparison with the CTE of copper, which is the first plating layer on the plastic. And the high moisture absorption of poliyamides makes it even more difficult.
Enough said about the problem, let’s talk about the solution now. In a nutshell, here are the results:
Qualified series parts with fine pitch: LCP, PA4T, PC/PET and thermoset.
- Parts dimensions from few mm to several cm
- Fine pitch line/spacing: 150/150 micron (in certain cases 80/80 micron)
- In the case of the LCP material, the metallized circuit has gone through welding lines
Performed tests:
- 1000 h at 85°C/85% RH
- 1000 h -40°C – 140°C (temperature cycling)
- Scotch tape test after the respective environmental tests
All parts passed the tests without any cracks and without any delamination.
How was the solution found?
A fundamental principle in finding a solution is the following: In order to find a reliable solution, you must first understand the mechanisms that lead to the problem, and you can assume that you has understood these mechanisms, only if you can reproduce the problem (and this not only for one time). Otherwise it often happens that one believes that one already has a solution, only to discover after a while that the problem has reappeared with the same or similar phenomena.
Based on the above-mentioned principle, we took on the subject of cracks and ablations, and we got to the root causes of their formation mechanisms, and we were able to prove this reproducibly in repeated life tests.
The solution cannot be traced back to the elimination of a single cause, it is rather the interaction of many factors and, as is so often the case, process interfaces play an important role. To put it simply, to get a reliable MID part you have to start with injection molding and end with packaging of the parts. Nonetheless, in the case of cracks and ablations, one process is of enormous importance for reliability and that is metallization.
Why just the metallization process?
Because this is where the biggest influencing factor lies, namely the difference between the CTE of the metallization and the plastic. Here you have two options, either you bring the CTE of the plastic down or the CTE of the metal layer higher. In many experiments we have succeeded in developing a metallization process that, in short, has reduced the CTE of the plating. We also had many additional positive effects that increased the stability of the metallization process and drastically reduced the process costs.
That sounds like a very complex process, one would think?! The answer is definitely “not”, the process has been totally simplified. In this context I recall a saying from the brilliant Russian writer Leo Tolstoy: “There are always the simplest ideas that have extraordinary success”.
More about the above-mentioned metallization process and the cost savings achieved with it will be published later in a separate post.
Kind regards and best wishes
Nouhad
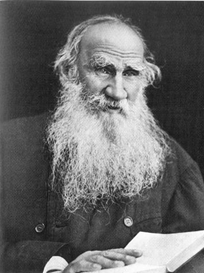